Bockman’s Bites on Lean Six Sigma in Additive Manufacturing Last Chapter
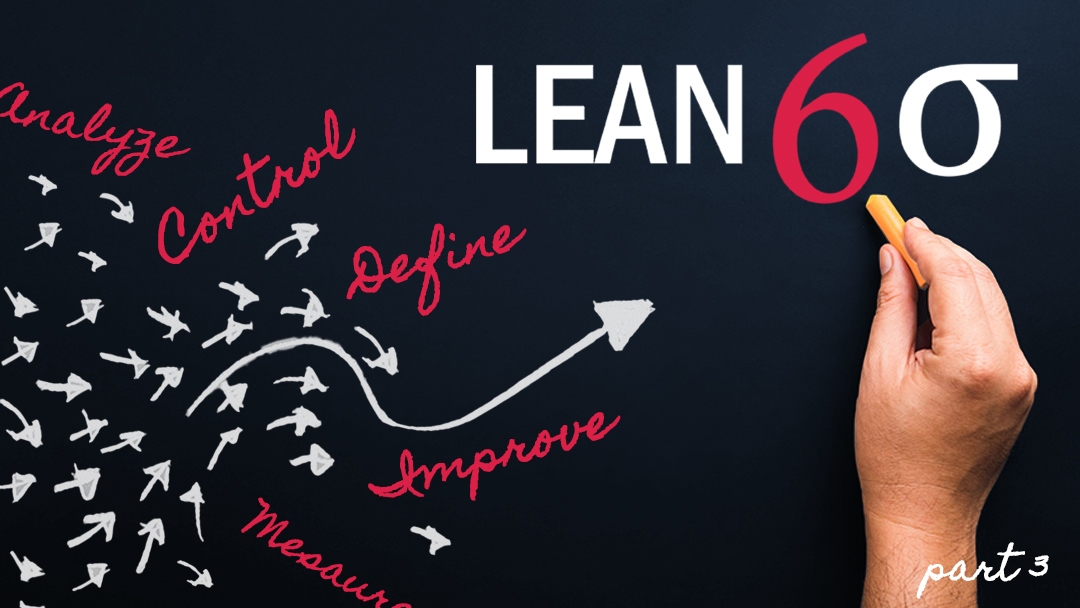
Welcome back to Bockman’s Bites … now, on to the last one...
The bedrock principle of Lean Six Sigma is to reduce waste by evaluating DOWNTIME or Defects, Overproduction, Waiting, Non-Utilized Talent, Transportation, Inventory, Motion, and Extra Processing. If you’re familiar with additive manufacturing then you know that these same principles can be applied more often than we care to admit. However, there are solutions that will lead to process improvements.
It’s important to remember the DMAIC model in Six Sigma and that’s where I start when approaching a customer who already has components of a workflow. Understanding the outcomes expected, but first baselining and process mapping the entire workflow looking for those gaps is first and foremost.
The next generation of industrialization is committed to an agile manufacturing approach. Defined by the ability to quickly respond to customer production needs, agile manufacturing embraces AM and integrates sophisticated software tools to enhance productivity. If we combine that with the Lean Six Sigma concept, then we can begin addressing immediate concerns with AM and solve problems like supply chain resiliency.
Production Planning | Having access to a centralized Enterprise Resource Planning (ERP) software solution capable of organizing AM technologies and material capabilities across multiple facilities enables production specialists to quickly print parts and immediately service customer needs. Oftentimes referred to as on demand manufacturing, this process eliminates the need for warehousing and will completely transform the traditional supply chain that constantly faces logistical nightmares (tariffs, long lead times, emissions). This creates a significant opportunity for repair and spare part providers to locally produce parts for aviation, transportation and defense products that cannot afford equipment downtime.
Maximize Throughput | Data is key to improving workflows. Management Execution Systems (MES) are designed to connect, track and monitor complex systems to ensure operational efficiency and improve production output. Having an integrated software that seamlessly connects conventional manufacturing with AM enables engineering teams to quickly assess technology benefits and assign production requests using time, quality and cost metrics. With the right software, engineers can identify AM ready parts, develop cost assessments and provide complete production transparency to management. It’s a strategic communication tool that relies on data and connectivity.
Conclusion
Maximizing the benefits of Lean Six Sigma takes an entire organization into consideration, encompassing hardware, software, processes and people. Is one more important than another when it comes to overall productivity? Not necessarily, but I argue that a sophisticated software solution cannot be underestimated and can likely become the backbone to process improvement. Reducing waste, eliminating downtime and enhancing throughput all relies on accurate data and production transparency. Ask yourself, how are you reducing waste in your process? What type of data do you use to justify decisions?
At 3D Control Systems, we are tackling this head on and invite you to learn more about our software solutions that are addressing the problems of today and proactively preparing for ones of tomorrow.