The Hidden Costs of 3D Printing
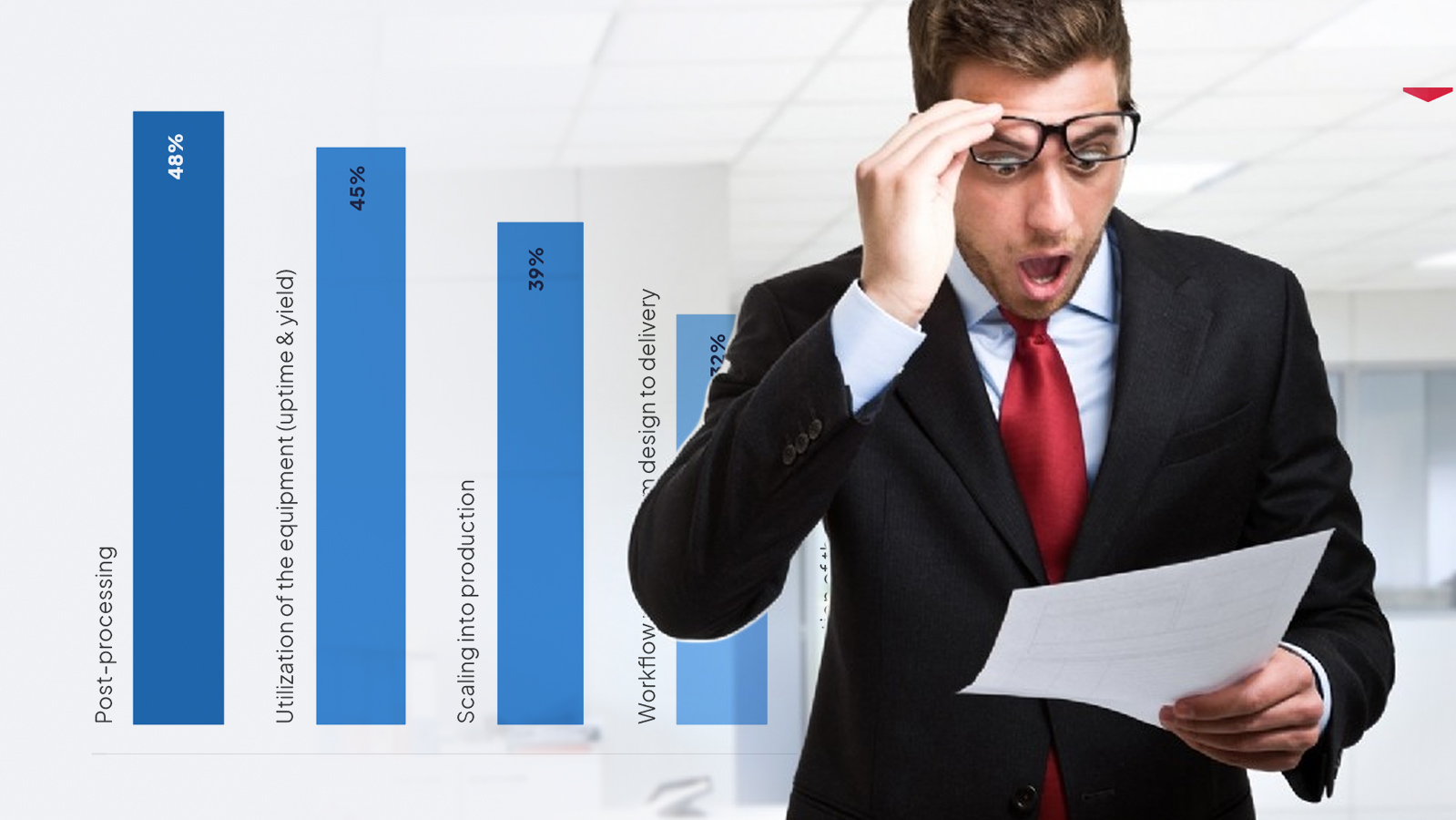
When it comes to 3D printing, we’re all eager to leverage the benefits of advanced manufacturing. The technology promises faster time-to-market, a better product development cycle, and new capabilities like mass customization and complex geometries. Of course, it’s not all a bed of roses; on top of overhyped promises and ongoing growth in areas like materials availability, bringing additive manufacturing into a workflow comes with a series of hidden costs.
Some of the costs of investing into a new technology are obvious. Capital expenditure to buy and operate the equipment, workforce training, and general system upkeep and maintenance are familiar to anyone in manufacturing. But 3D printing has what may be some unforeseen costs that we need to talk about more openly.
In a recent table talk at an ASME virtual event, I had the opportunity to address just this. During the talk, I asked what those joining that day thought were the greatest or biggest hidden costs in 3D printing -- and the results weren’t necessarily what our team was expecting to hear.
In order of importance by vote, some of the biggest hidden costs of 3D printing are:
We had also offered a tenth option -- service contracts -- that didn’t get any votes at all.
Some of these areas, while still “hidden” from new adopters, aren’t surprising. Post-processing, for example, has long been called the “dirty little secret of 3D printing.” Removing supports, depowdering/washing, debinding, sintering, curing, polishing, smoothing, machining, painting: the processes involved after a build finishes on the 3D printer can be incredibly time-consuming -- and expensive.
Other areas, like material cost, may also not be the most surprising. Input materials will obviously be a pretty constant need for a 3D printer to continue running; you can’t build something out of nothing, after all. Still, the costs for many 3D printable materials are often higher than their traditionally manufacturable counterparts. 3D printing feedstocks must be specifically formulated for 3D printing. In metal processes, for example, you can’t just add any standard aluminum powder into a powder bed fusion 3D printer and expect it to work; the material has to be tuned to the specific process and, often, machine where it will be used. Further, many standard manufacturing materials still haven’t been converted to a 3D printable form; PVC is among the most commonly used plastics in general manufacturing and 3D printing options remain very limited, as just one example. Engineering-grade materials are also relatively scarce and, even when they are available, are often priced at a premium.
Digging in further to the areas that might surprise new adopters the most, though, we weren’t surprised to see workflow processes bring in about one-third of the votes.
The end-to-end design-to-delivery process of manufacturing via 3D printing is complex. From design for additive manufacturing (DfAM) requiring specialty know-how to coordinating every step of the additive manufacturing process while avoiding bottlenecks, all while maintaining quality, repeatability, and predictability in an IP-secured framework -- there are a lot of considerations to take into account.
Targeting pain points like that is where we come in.
We founded 3D Control Systems specifically to create an easily adoptable, easily implementable, easily maintainable, easily customizable, and easily scalable advanced manufacturing workflow. Our first product, 3DPrinterOS, introduced the concept of technology-agnostic, cloud-based workflow management for 3D printing. Since 2014, more than 140,000 users around the world have turned to 3DPrinterOS for a solution.
In 2021, we introduced a wider-reaching workflow control system with ZAP.am.
Using our platform takes the surprise and guesswork out of your advanced manufacturing workflow. At every step of the way, you can see with full transparency and security exactly what is happening. With traceability built in, there won’t be any surprises later on down the road, either.
Understanding the needs of your workflow is a critical step to making your workflow work for you.
Interested in finding out more how we can help? Let’s start a conversation today.
Michelle Bockman