What is the Factory of the Future?
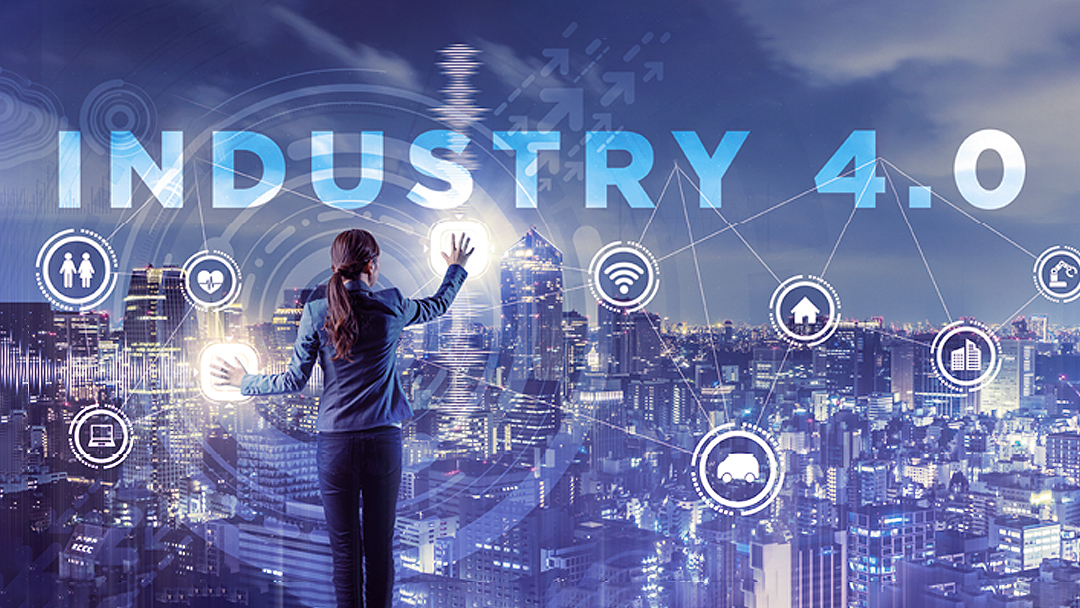
Transforming the conventional machine shop to a fully-connected, digital production facility that champions data and equipment connectivity.
Introduction
Boston Consulting Group defines the Factory of the Future as a vision for how manufacturers should enhance production by making improvements in three dimensions: plant structure, plant digitization and plant processes. As we enter the next generation of industrialization, many manufacturers are actively embracing Industry 4.0 and identifying ways to incorporate automation, artificial intelligence, additive manufacturing and data to fully maximize equipment capabilities and potential. The challenge is that many conventional machine shops are equipped with a variety of subtractive, additive or other manufacturing processes and are unsure how to connect the technologies or optimize workflows to improve efficiency.
So what’s the solution? The answer isn’t singular and likely more complex depending on your facility capabilities and technical expertise. However, we hypothesize that machine connectivity and streamlined communications through data is a great first step in the right direction. Using the BCG definition of the Factory of the Future, we demonstrate how workflow software can maximize productivity and generate new opportunities.
Plant Structure
Economic and environmental sustainability are key focuses for the next generation of manufacturing. In my experience, it’s important to examine existing processes, tear them apart and rebuild in a way that improves customer relationships and financial outcomes. For example, the automotive industry is transitioning from lean manufacturing to agile manufacturing, which embraces on-demand production and eliminates the need for warehousing. Because of this, many automotive OEMs are locally machining or printing parts to service regional requests. This reduces their carbon footprint and removes the logistical nightmares associated with the typical supply chain.
The challenge is accessing and managing a decentralized manufacturing network to reliably machine and produce parts that are within spec and meet customer requirements. The solution is a fully integrated, centralized software that provides complete line of sight capabilities that track, monitor, and audit every part being produced.
Plant Digitization
Intelligent manufacturing depends on data and the digitization of assets, parts, technologies, materials, etc. As the adoption rates for AM continue to increase so does the need for a sophisticated solution that organizes equipment capabilities, material compatibility and resource management. As a former practicing engineer and business manager tasked with the responsibility to make process improvements, I understand the value of reliable data and how critical it can be to the bottom line.
3D Control Systems solves this by introducing the World’s first operating system that is compatible with CNC machining and 3D printing. Made possible with a browser-based cloud software solution, engineers can develop a digital library of CAD files and immediately assign projects to specific manufacturing equipment. This is highly relevant for production facilities, manufacturers, machine shops and universities. For example,Duke University and ZAP, an impressive inhouse machine shop capable of 3D printing, CNC machining, laser cutting and even using robotic arms, adopted the cloud platform to digitally connect the machines and manage jobs. Used as a hub for startup companies to access different technologies to prototype or produce parts, ZAP is now capable of 3D printing 15,000+ hours per week and recently added another 100 3D printers to the network enabling access to 5,000+ students and startups.
Plant Processes
The completion of the digital thread with the successful integration of workflow software maximizes and supports a streamlined communication system that is transparent and accessible. As a business executive with years managing teams and resources, I cannot underestimate how valuable it is to effectively communicate horizontally across departments and vertically to upper management. Not only does this enhance operational productivity, it simultaneously provides a competitive advantage to advance customer relationships. For example, having access to real-time production data enables supply chain managers to immediately react to customer requests or needs. This is the definition of just-in-time (JIT) manufacturing. It may be an old concept but it works.
Conclusion
The Factory of the Future relies on machine connectivity, data and streamlined communications that simplifies production and enhances customer relationships. After all, the businesses that remain customer-centric and are willing to continuously improve will inevitably win the day. What steps is your machine shop or manufacturing facility taking today to be economically and environmentally sustainable for the future? How has your campus or research facility embraced digitization for process improvement? Why haven’t you adopted an integrated software solution that makes customer acquisition easier or retention more profitable?
We invite you to take a moment to learn more about 3D Control Systems and how 3DPrinterOS is #1 rated Cloud 3D Printer Management software by top universities.