Bockman’s Bites on Lean Six Sigma in Additive Manufacturing Part 1
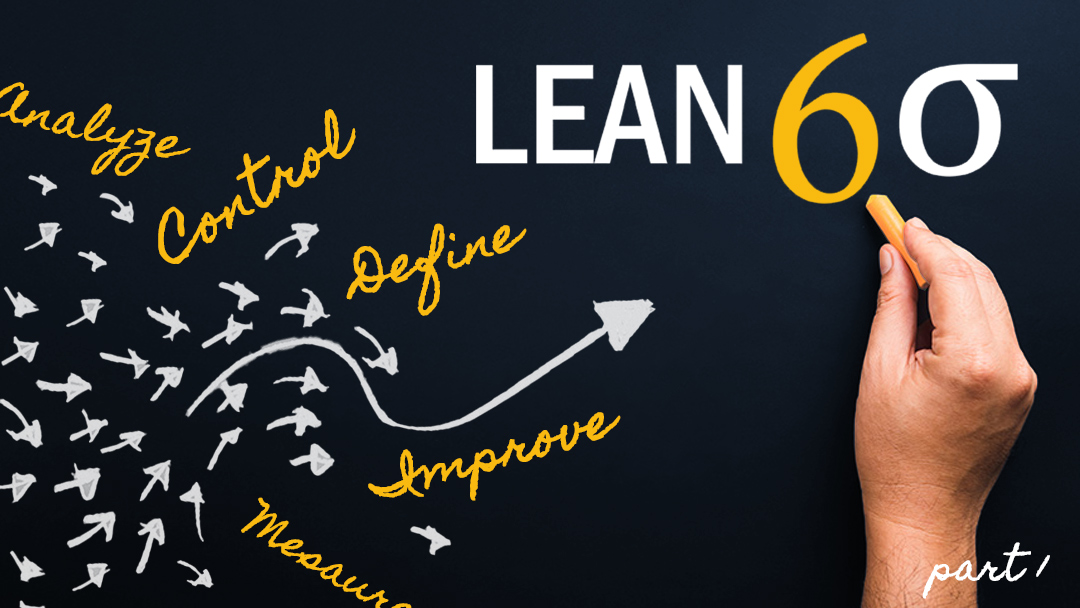
Bockman’s Bites on Lean Six Sigma in Additive Manufacturing
Trim the fat. Cut your losses. Eliminate Muda.
I am writing a short series of bites about the importance of implementing Lean Six Sigma methodology in Additive Manufacturing. It not only drives efficiencies and increase output, but it can improve quality levels as well.
I will open up the first bite with the background of what L6S is in traditional manufacturing and some of my experience.
Bite I : What is Lean Six Sigma and AM Combined?
Continuous improvements for any department of an organization are paramount to the successful growth and adaptation of a business. In our hyper competitive commercial and industrial marketplace there is no excuse for downtime, so what steps are you taking today to maximize organizational or production efficiency?
Lean Six Sigma is a managerial concept born from the combination of lean manufacturing and Six Sigma aimed to identify operational weaknesses, expose variation and make adjustments for continuous improvements. While each concept was used separately during the 1980’s and 90’s primarily for automotive and electronics manufacturing, it became a joint idea during the early 2000’s and has since transformed manufacturing. With the ultimate intention to identify weaknesses and improve operational efficiency, Lean Six Sigma has become a significant tool across many different industries and professions. In my own experience at General Electric, L6S was a part of our culture, our DNA. I had the privilege to work with a Lean Sensei, who helped us learn and apply methodologies in our manufacturing plants. We made real improvements by identifying ways to remove unnecessary steps in our workflow and eliminate muda (waste). With my knowledge of Lean Six Sigma and a decade of implementation experience, I’m turning my sights towards additive manufacturing. What needs to be done in order to fully optimize AM and the future of manufacturing? Can L6S work in additive manufacturing?
The additive manufacturing (AM) industry is relatively young. However, there are countless hardware, software, technology and material companies popping up everyday and making significant impacts. For reference, the AM market is expected to exceed $20 billion by 2023. Alternatively, the CNC market was valued at approximately $7.87 billion in 2020, further indicating that AM is certainly here to stay. But we haven’t figured out all the kinks yet.
L6S is about efficiency. AM has already proven itself as a viable prototyping and production unit but what steps can be taken to truly maximize utilization? While 3D printing is a revolutionary piece of hardware technology, the brains and machine connectivity within a machine shop or manufacturing space is average at best. Smart manufacturing relies on actionable information collected through key data points and must be driven by intelligent systems. For example, contract manufacturing service providers in the US have grown significantly and are desperate for a software platform that allows them to digitally view the production floor, assign projects, and proactively identify problems (failed builds, predictive maintenance, equipment downtime). Simply put, how can we make additive manufacturing smarter? Check back in next week for our next installment of L6S-AM when we address the challenge of combining conventional manufacturing methods and what that means for certain industries.
Feel free to share comments, your experience and where you think it’s headed.